- Что такое SMED
- Его преимущества перед обычным методом
- Основные принципы SMED
- Пошаговый план внедрения
- Инструменты и техники
- Распространенные ошибки внедрения
- Связь с другими методологиями
- Коротко о главном
Прибыль производственного предприятия зависит от количества произведенной продукции, ее себестоимости, простоя оборудования и расходов на издержки. Если производство небольшое или выпускает товары небольшими партиями, для выпуска нового товара нужно перенастроить оборудование и подготовить все необходимое. Это время называется простоем, и чем оно дольше, тем больше прибыли компания недополучает. Сократить время переналадки может метод бережливого производства SMED.
В статье рассказываю, как работает метод быстрой переналадки оборудования, в чем его преимущества и как его внедрить себе на производство.
Что такое SMED
Метод быстрой переналадки (SMED, от англ. Single-Minute Exchange of Die) — это система для сокращения времени переналадки оборудования и быстрого перехода от производства одной продукции к другой. Дословно термин переводится как переналадка за одну минуту, но выражение это образное и означает просто очень быструю смену технологического оборудования за минимально возможное время.
SMED был предложен японским инженером Сигэо Синго в 1950-х годах. Синго был одним из ключевых персон в развитии систем управления качеством и производственными процессами в таких компаниях как Toyota.
Метод хорошо подходит компаниям, которые выпускают большой ассортимент продукции или изготавливают небольшие партии товара. Он помогает сократить время простоя оборудования, увеличить гибкость производственного процесса и оперативно подстраиваться под изменчивый спрос на продукцию. Практикуется в концепции бережливого производства.
Бережливое производство — это философия организации производства, при которой конечный продукт максимально удовлетворяет потребности клиентов с минимальными затратами ресурсов на организацию производства и издержки.
Метод SMED и философия бережливого производства взаимодополняют друг друга и служат инструментами для повышения конкурентоспособности современных предприятий.
Простыми словами, SMED — это быстрая переналадка оборудования.
Преимущества SMED по сравнению с обычным способом переналадки
Метод быстрой переналадки |
Обычная переналадка |
|
Время переналадки |
Может быть сокращено до менее чем 10 минут |
Обычно занимает от 30 минут до нескольких часов или даже дней при сложном или крупногабаритном производстве |
Гибкость производства |
Производство может быстро перенастраиваться на другие продукты, модели, рецептуры, может производить любые товары даже мелкими партиями |
Сложный и длительный процесс переналадки, сложно работать с большим количеством мелких партий |
Затраты на простои оборудования |
Минимальные затраты за счет меньшего времени простоя |
Высокие затраты на простои из-за длительных переналадок |
Подготовка персонала |
Внедрение метода требует дополнительного обучения |
Уделяется меньше внимания обучению сотрудников |
Используемые инструменты |
Процессы максимально стандартизированы, упрощены и отлажены как часы |
Процессы не структурированы, не стандартизированы и выполняются «как получается» |
Участие персонала |
Персонал вовлечен в процессы и имеет высокий уровень инициативы |
Персонал заинтересован средне, поручения выполняются по указаниям сверху |
Управление запасами и ресурсами |
Производительность повышается — управлять запасами становится эффективнее и более прогнозируемо, не хранится лишних запасов |
Возможны излишние запасы из-за неопределенности в производственных процессах |
Качество продукции |
Качество остается на стабильно высоком уровне за счет отлаженных и стандартизированных процессов |
Качество может быть нестабильным из-за не отлаженности процессов |
Внедрение изменений |
Легко внедрять изменения и улучшения |
Сложно внедрять изменения, работники к ним не привыкли и сопротивляются |
Количество брака |
Частые переналадки оборудования обеспечивают постоянную донастройку и контроль, уменьшают сбои. В продукции встречается меньший процент брака |
Редкие переналадки дают меньший контроль за оборудованием и более частые сбои в работе. В продукции встречается больший процент брака |
Основные принципы SMED
Наблюдая за работой разных производств, создатель метода Сигео Синго подметил, что все процессы переналадки можно разделить на две категории:
- Внутренние.
- Внешние.
Внутренние процессы требуют полной остановки работы оборудования и именно из них формируется время простоя и связанные с этим убытки. Например, заменить пресс-форму для печати деталей или комплектующих невозможно без остановки станка.
Внешние процессы переналадки могут делаться без остановки оборудования, и именно они способны сократить время простоя. Если упростить, внешние процессы — это больше про подготовку к переналадке. Например, подобрать крепления, принести детали, подготовить необходимое — все это можно сделать параллельно с работой оборудования, не останавливая его.
На основе этих двух видов процессов Сигео Синго сформулировал 8 методов и принципов:
- Отделение внутренних операций от внешних. Принцип предполагает четкое разделение всех операций на внутренние и внешние. Внешние операции можно делать, не останавливая процессы, что минимизирует время простоя.
- Перевод максимального количество действий на внутренних процессах к внешним. Операции, которые раньше требовали полной остановки оборудования, критически оцениваются, и все возможные этапы и действия максимально переводятся в категорию внешних. Например, подготовка инвентаря и инструментов выполняется до начала перенастройки.
- Стандартизация функций. Все процессы должны быть приведены к единообразию, иметь инструкции и стандарты. Четкость действий значительно облегчает процессы для сотрудников и ускоряет время переналадки.
- Упрощение крепежа. Крепежные элементы должны быть максимально простыми в использовании и быть для всех операций одинаковыми или единообразными. Использование быстрозажимных механизмов позволяет существенно сократить время, затрачиваемое на установку и замену. Упрощение крепежа снижает вероятность ошибок в процессе перенастройки и делает его более безопасным и надежным.
- Использование промежуточных приспособлений. Принцип предлагает использовать вспомогательные или временные приспособления, которые облегчат или ускорят переналадку. Приспособления позволяют заранее подготовить инструменты и материалы и сократить время, необходимое для их замены на оборудовании.
- Параллельные операции. Все процессы переналадки должны быть проанализированы, прописана их очередность и взаимосвязи. После анализа будут выделены задачи, которые можно выполнять параллельно друг с другом или параллельно с работой оборудования.
- Устранение корректировок. Согласно принципу стоит максимально снижать необходимость корректировок после перенастройки оборудования и больше уделять времени следованию стандартов, действиям четко по инструкциям и подготовке к переналадке.
- Механизация. Ускорить процессы и уменьшить физический труд можно, внедрив автоматизацию и механизацию. Это может включать в себя использование автоматических систем для перенастройки или вспомогательного оборудования.
Пошаговый план внедрения SMED
Внедрение метода SMED — это комплексный процесс, требующий подготовки, тщательного анализа, планирования действий и вовлечения всех участников производственного процесса. Разберем по шагам, как правильно его провести.
Шаг 1. Наблюдение и анализ текущих процессов переналадки
Задача первого шага — изучить текущие процессы, зафиксировать временные затраты и составить список всех операций и процессов переналадки.
Помочь в этом могут личные наблюдения, системы видеофиксации, опросы и анкетирование сотрудников.
После сбора информации проводится анализ на то:
- какой этап занимает больше всего времени;
- какие причины простоев возникают;
- как процесс может быть улучшен.
Дополнительно со сбором информации стоит зафиксировать наблюдения, пожелания и комментарии от непосредственно задействованных в процессе специалистов. Часто эта информация становится основой для будущей автоматизации и подкидывает много хороших идей по улучшению.
Шаг 2. Выделение внутренних и внешних операций
Когда все операции изучены и зафиксированы, стоит прописать, какие из них могут выполняться без остановки оборудования (внешние), а для каких остановка — это обязательное условие (внутренние).
Анализируя полученные данные, стоит отметить, какие из внутренних операций могут быть переведены на внешние. Например, при переналадке у сотрудников уходит время на то, чтобы принести инструменты, детали, крепежи. Можно сделать это заранее во время работы станка.
Шаг 3. Преобразование внутренних операций во внешние
Этап направлен на максимальное увеличение внешних операций. Этого можно добиться, подготовив заранее нужные комплекты инструментов, используя однотипные детали и комплектующие, универсальные инструменты и оснастку и написав четкие инструкции и стандарты.
Шаг 4. Оптимизация всех операций
После определения того, какие операции могут быть выполнены заранее, следующим шагом будет оптимизация всех операций. Это можно выполнить тремя способами или их комбинацией, в зависимости от процесса и его особенностей:
- Максимально упростить процесс.
- Стандартизировать процесс.
- Внедрить параллельное выполнение процесса с другими.
При внедрении параллельного выполнения задач по переналадке несколько сотрудников могут одновременно выполнять разные задачи по подготовке и переналадке.
Для лучшей визуализации можно использовать систему организации рабочих процессов Kanban и метод организации рабочего места по системе 5S: сортировка, рациональное расположение, уборка, стандартизация и совершенствование.
Шаг 5. Создание документации и обучение персонала
В методе SMED важнейшая составляющая — это люди, их вовлеченность и заинтересованность в улучшении и оптимизации процессов. После того, как процессы перестроены и найдены оптимальные решения для ускорения переналадки, все нужно задокументировать и написать простые пошаговые инструкции для персонала.
Все сотрудники должны знать:
- какие изменения были внесены в процессы;
- каковы новые стандарты;
- как правильно по-новому выполнять процессы;
- какова последовательность работ;
- что выполняется в параллель;
- кто за что ответственный.
Когда документация и стандарты готовы, сотрудников надо обучить, объяснить все на примерах и помочь применить знания на практике во время воркшопов. Чтобы закрепить изменения, можно создать рабочую группу ответственных, которые будет контролировать и мониторить процесс изменений. Не лишним будет периодически устраивать рабочие собрания для обмена мнениями и отзывами, на них сотрудники могут подсказать новые места для улучшений или предложить варианты корректировки текущих процессов.
Инструменты и техники для внедрения SMED
Облегчить перестройку процессов и ускорить процессы переналадки может использование дополнительных инструментов, методов и систем организации рабочего процесса. Рассмотрим наиболее подходящие для метода SMED.
Диаграмма спагетти
Инструмент с необычным названием хорошо визуализирует траектории перемещения работников между станками, отделами или рабочими местами. На диаграмме можно заметить как передвижение людей (например, один работник нажал кнопку на одном станке, потом переместился и нажал на механизм другого станка), так и передвижения материалов и комплектующих (например, откуда сотрудник принес материал, как далеко он расположен от станка, какие препятствия сотрудник обходит во время пути) в производственном пространстве.
Диаграмма визуализирует:
- избыточные или неэффективные перемещения;
- оптимальное или не оптимальное расположение оборудования и материалов;
- показывает «узкие» места и точки скопления
Собрать данные для построения диаграммы можно с помощью видеофиксации процессов и личного наблюдения за работой производства на протяжении нескольких смен работы.
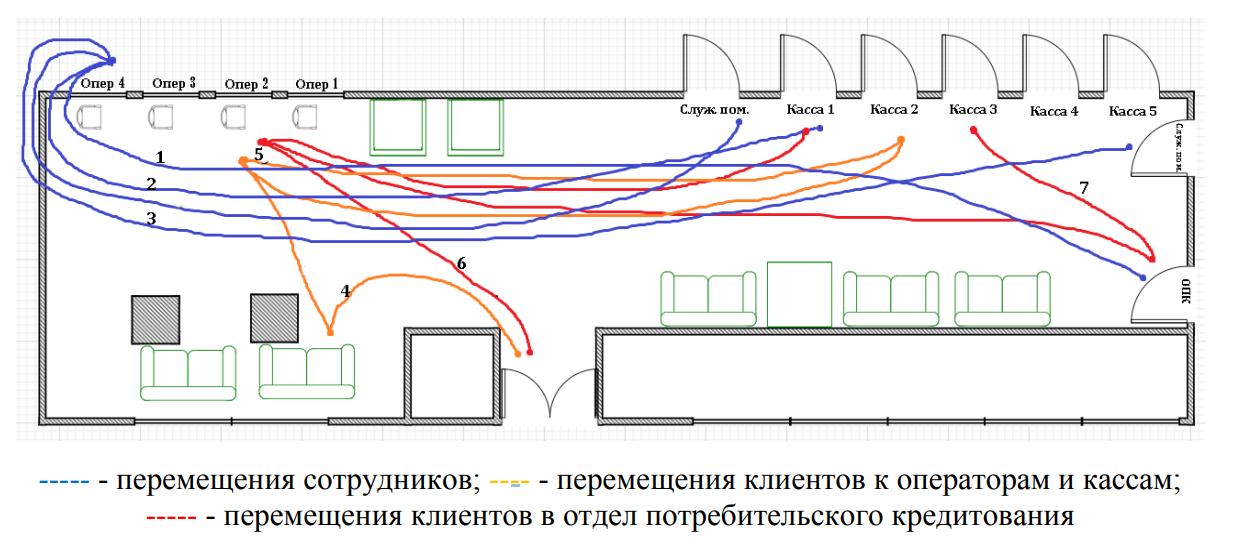
Этот инструмент идеально подходит для этапа «Наблюдение и анализ текущих процессов» и выделения операций в категорию внутренних или внешних.
Видеозапись процессов
Запись операций помогает детально проанализировать каждое действие, выполняемое операторами. Это отлично визуализирует и подсвечивает излишние шаги и дублирующие действия.
Видеозапись служит отличным обучающим материалом для новых сотрудников, демонстрирует стандартизированные процедуры и позволяет быстрее освоить необходимые навыки, показывая процессы на живом примере. Повторный просмотр записанных процессов предоставляет возможность команде провести совместный анализ и обсудить возможные улучшения во время мозгового штурма.
Анализ временных затрат
Подход позволяет выявить критически важные этапы, на которых возможно сократить время переналадки, а также определить, какие действия сотрудников требуют улучшения или автоматизации.
Анализ временных затрат дает четкое представление о том, какие части процесса можно оптимизировать для повышения общей производительности труда.
Методология 5S
Методология 5S предлагает 5 действий и принципов для организации рабочего места и продуктивной рабочей среды:
- Sort — сортировка.
- Set in order — систематизация и рациональное расположение.
- Shine — уборка.
- Standardize — стандартизация.
- Sustain — совершенствование.
Методология помогает создать рабочее пространство где всегда чисто, все необходимое в быстром доступе, а все лишнее — убрано или выкинуто. Работники в такой среде быстрее ориентируются и выполняют рабочие задачи.
Распространенные ошибки при внедрении SMED
- Непонимание концепции SMED. Команда может не понимать принципы SMED и его ценность для внедрения. Это может вызвать сопротивление и проблемы внедрения.
- Недостаточная подготовка сотрудников. Необученные сотрудники также склонны сопротивляться изменениям, допускают много ошибок и повышают процент брака в работе.
- Игнорирование анализа текущих процессов. Внедрение изменений без понимания текущего состояния процессов способно больше навредить, чем помочь.
- Пренебрежение документированием новых процессов. Без документации и инструкций стандарты могут не соблюдаться и процесс станет неэффективным.
- Недостаток необходимых инструментов и материалов. Отсутствие необходимого оборудования и оснастки во время переналадки может привести к еще большим временным задержкам.
- Фокус только на скорости. Фокусировка сотрудников на уменьшении времени переналадки любой ценой может повысить качество выпускаемой продукции и процент брака.
Связь с другими методологиями
Метод переналадки SMED тесно связан с другими методологиями бережливого производства, такими как Канбан, Кайдзен и TPM. Они все ставят своей целью улучшение, автоматизацию и оптимизацию процессов, а также уменьшение потерь и издержек.
Кайдзен
Сокращение времени переналадки, которое предлагает SMED, служит ярким примером Кайдзен-инициатив, направленных на повышение продуктивности производства и вовлечение сотрудников в непрерывный процесс улучшения.
Канбан
Канбан помогает наглядно визуализировать процессы и организовать слаженную работу. Упрощение процессов, достигнутое через SMED, позволяет быстрее реагировать на изменения в спросе, оптимизировать работу с запасами и повысить гибкость производственного процесса.
Изменения в спросе — это ситуация, при которой например в день A были две больших партии товара и на изготовление и нужна была всего одна переналадка для переключения, а в день Б поступила задача выполнить 7 маленьких партий и между ними нужно большое количество переналадок.
TPM (Total Productive Maintenance)
TPM фокусируется на повышении общей эффективности оборудования через регулярное техническое обслуживание и вовлечение сотрудников в поддержание состояния машин. SMED дополняет TPM, уменьшение времени переналадки позволяет лучше использовать время работы оборудования и сокращать простои.
Коротко о главном
- Метод SMED значительно сокращает время переналадки оборудования, что позволяет повысить производительность и снизить издержки на производстве.
- Внедрение метода способствует повышению гибкости производственного процесса, позволяя быстрее реагировать на изменения спроса и увеличивать производимый ассортимент продукции.
- После внедрения метода процесс переналадки становится прозрачным и структурированным.